Установка для нанесения тонкопленочного электролита на твердооксидные топливные элементы
Установка для нанесения тонкопленочного электролита на твердооксидные топливные элементы
Оборудование стоимостью в несколько десятков миллионов рублей разработано в Институте сильноточной электроники СО РАН по заказу промышленного партнера – инновационного центра «Бирюч» (группа компаний «ЭФКО»). Установка станет частью производственной линии этой научно-производственной компании в Белгородской области и будет использоваться для изготовления топливных элементов для энергетического сектора и беспилотных авиационных систем.
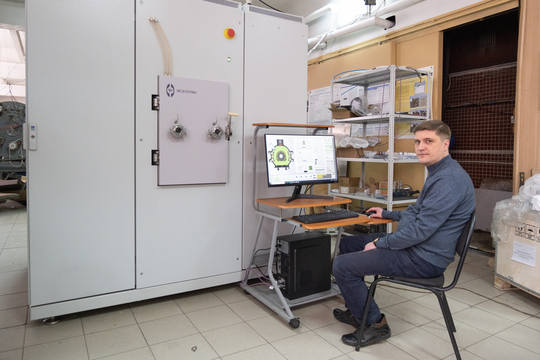
– Твердооксидные топливные элементы лежат в основе перспективных электрохимических генераторов, которые позволяют получать электрическую энергию путем прямого преобразования энергии химического топлива (водорода или водородсодержащего газа, например, получаемого из метана), – объясняет Андрей Соловьев, зав. лабораторией прикладной электроники. – При соединении топлива с окислителем (обычным воздухом) в топливном элементе происходит химическая реакция, в результате которой на выходе получается электричество и чистая вода.
По словам Андрея Александровича, обычные способы получения электроэнергии имеют небольшой коэффициент полезного действия, всего около 20–30 процентов, в то время как генераторы на основе твердооксидных топливных элементов позволят получать электроэнергию с КПД не менее 50–60 процентов. Другим их достоинством является экологичность (крайне низкие выбросы вредных газов в атмосферу). Эти устройства могут быть как мобильными, так и стационарными, а в будущем на их основе могут строиться даже электростанции. Они очень востребованы в водородной энергетике, где водород рассматривается как способ хранения электроэнергии.
Коллектив лаборатории прикладной электроники – единственный в России, где создана и успешно масштабирована для промышленного использования технология нанесения тонкопленочного электролита с помощью магнетронного распыления. Эти исследования ведутся в институте уже почти 20 лет. Ученым удалось добиться равномерного нанесения тончайших оксидных пленок на образцы разного размера – от изделия размером с монету до образцов размером 10 на 10 сантиметров. Как раз такого размера и будут топливные элементы планарной конструкции, из которых в дальнейшем будут собираться батареи (стеки) для энергоустановок.
Суть технологии состоит в следующем: на пористую керамическую пластину (анод), на которую будет подаваться топливо – водород, наносится газонепроницаемая пленка электролита толщиной около 5 микрон. Затем на электролит в виде тонкой пленки наносится третий компонент – катод, куда подается окислитель – воздух, и где образуются отрицательные ионы кислорода. Электролит при высоких температурах обладает свойством ионной проводимости, ионы кислорода перемешаются с катодной стороны на анодную через тонкую пленку электролита. С этой стороны и будет происходить реакция, в результате которой высвобождаются электроны, создающие электрический ток.
Оказывается, что чем тоньше пленка, тем большую мощность можно получить с одного квадратного сантиметра! Для нанесения пленок сейчас чаще всего используется оксиды циркония и церия, которые обладают оптимальным набором свойств, хотя ученые исследуют и возможности применения других оксидов.
Ученые из ИСЭ СО РАН в разные годы неоднократно выигрывали гранты РФФИ и РНФ, позволяющие развивать эту тематику, однако создание промышленного прототипа установки требовало крупных вложений и было возможно лишь при условии привлечения средств промпартнера. Договор с Инновационным центром «Бирюч» заключили в конце 2021 года, а сейчас томские исследователи уже готовят оборудование к отправке. На создание и сборку установки потребовалось полтора года!
Научный сотрудник Сергей Работкин демонстрирует установку: она состоит из источников питания, вакуумных насосов, систем подачи воды и газа и, конечно же, вакуумной камеры, где происходят основные процессы. Внутри нее находится барабан, куда могут одновременно поместиться 24 образца. При температуре около 400 градусов Цельсия внутри вакуумной камеры этот барабан вращается и со специальных устройств (магнетронных распылительных систем) ведется равномерное напыление пленки электролита.
Созданная в Томском академгородке установка станет частью производственной цепочки по изготовлению твердооксидных топливных элементов, которые могут использоваться в проектах, связанных с энергетикой, а также как источники питания беспилотных авиационных систем. Более подробно о последних можно узнать на сайте →. Как отметили исследователи, промпартнер планирует объединить в одной цепочке сразу несколько перспективных технологий.
Источник: Томский научный центр СО РАН.